19/12/2019 – From fibre back to fibre — auf Deutsch lesen
Pilot project “DiTex” trials high-quality textile recycling
Textiles are still mainly made from fresh fibres. A circular economy has largely not yet been established. This will change soon.
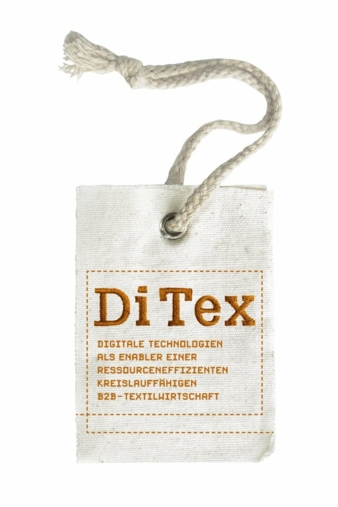
“DiTex – Digital Technologies as Enablers of a Resource-Efficient Circular B2B Textile Industry” is a research and development project related to the topic of “Resource-Efficient Circular Economies – Innovative Product Cycles” and is part of the “Research for Sustainable Development – FONA3” programme supported by the Federal Ministry of Education and Research. It will run from 2019 to 2022. © Hochschule Reutlingen
In a new research project, discarded garments or other textiles such as towels and bedlinen are seen as raw materials whose fibres can be extracted for new fabrics of the same quality.
In a rapidly growing textiles sector, this could prove an effective way to save resources and increase productivity. This is certainly the aim of the “DiTex” project, which is being conducted by the German Institute for Ecological Economy Research (IÖW) in collaboration with various partners. The project is funded by Germany’s Federal Ministry of Education and Research.
Starting point for a circular economy: textiles from bulk consumers such as hotels or restaurant chains
A major challenge in the recycling of textiles is knowing the exact composition of the fabrics. In the field of workwear, particularly in healthcare, hospitality and the police, textiles of similar compositions are used in huge volumes. German textiles companies Wilhelm Weishäupl from Munich and Dibella from Bocholt supply textiles to large-scale customers such as hospitals or restaurant chains. Both manufacturers are currently developing two textile product lines from recycled fibres. They will be tested by their customers in a one-year trial.
Digitisation for smart recycling: Intelligent label ensures information flow
The newly developed products are fitted with a “smart label” from Berlin-based start-up circular.fashion, which contains the fabric’s most relevant parameters such as the composition of the cotton and synthetic fibres. A database records available quantities of recycled materials. All participants involved in the textile cycle benefit from this digital information flow. “This label enables industrial laundries to determine, for example, which recycling companies will take a textile once it has reached the end of its lifecycle,” states textiles expert Ms Müller, shedding light on the possible logistics of recycling.
The project is being conducted by a research team from the Faculty of Textile and Design at Reutlingen University, the Hohenstein Institute for Textile Innovation and the ifeu institute for energy and environmental research in Heidelberg. The focus is on analysing the impact on quality, resources and sustainability of textiles included in the cycle. The findings will be made available free of charge to enable other companies to gain insights into the creation of a resource-efficient circular economy in the textiles industry.
Richard Harnisch
Institut für ökologische Wirtschaftsforschung GmbH, gemeinnützig