30/05/2022 – Techtextil: Monfort
Energy savings are more important than ever
Techtextil and Heimtextil Summer Special represent a once-only opportunity for Monforts to showcase its advanced finishing and coating technologies for two of its major markets.
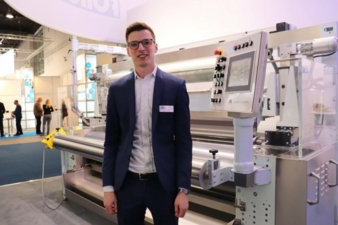
“Montex stenters provide maximum efficiency, the ultimate in flexibility and the ability to switch quickly from one fabric formula to the next,” says Monforts Textile Technologies Engineer Jonas Beisel. “The easy to use human-machine interface (HMI) makes the operation of the line much simpler and cuts down the necessary training periods, while at the same time reducing the chance of human error.” © Monforts
European-built Montex stenters have earned their leading position on the market for fabric finishing due to their robustness, reliability and economy. Existing customers include many manufacturers in the field of home textiles, as well as those making geotextiles, automotive fabrics and other functional materials. Dedicated Montex lines have also been supplied to producers of airbags, flame retardant barrier fabrics and spacer fabrics, as well as high-temperature filter materials.
Enery and heat recovery with Montex stenters
Energy prices are rising steeply everywhere and a particular emphasis for Monforts in Frankfurt will be on the energy and heat recovery that can be achieved with Montex stenters, through features such as better insulation of the treatment chambers or the MonforClean system, in which waste heat from the drying process is used to pre-heat the drying air resulting in a radical reduction in the conventional heat supply required compared to gas and thermal oil heating. The modular system for heat recovery can also be extended for exhaust air cleaning and odour elimination. Monforts can provide a range of further resource-saving and energy recovery options tailored to each individual line installation including modification of the heating source.
With the highly intuitive Qualitex 800 visualization software, all article-specific settings can be stored and the formulations for thousands of treatment processes called up again at any time. Individual operators can also personalise their dashboards with the most important machine functions and process parameters.
The Qualitex 800 system is available for the automatic and continuous operation of the company’s Montex stenters, as well as its Thermex continuous dyeing ranges, Monfortex shrinking systems and Montex®Coat coating units.
Expert finishing for different materials
Monforts Montex Coat coating units serve an equally diverse number of markets, including tents, tarpaulins and awnings, black-out roller blinds and sail cloth, automotive interior fabrics and medical disposables. Full PVC coatings, pigment dyeing or minimal application surface and low penetration treatments and solvent coatings (in explosion-proof conditions) with knife coating, roller coating or screen printing can all be accommodated with this system.
All of these very different materials require expert coating and finishing for maximum efficiency, using Monforts technologies which provide flexibility and the ability to switch quickly from one fabric run to the next, without compromising on the economical use of energy or raw materials.
The Monforts EcoApplicator offers further potential for sustainably achieving perfect finishes via a precise direct application system, as an alternative to conventional padding – where fabrics are immersed in a bath of the required finishing chemicals. It can significantly further reduce the energy and water required and finishes can be applied on just one side of the fabric, or both, and even separately on each side, to be sealed in place via different heating zones in the stenter. This allows endless differentiation possibilities.