03/07/2020 – Faster, more flexible and energy-saving — auf Deutsch lesen
Weber Ultrasonics: Ultrasonic laminating
One of the largest European producers of nonwoven fabrics and their end products relies on ultrasonic welding with technology from Weber Ultrasonics.
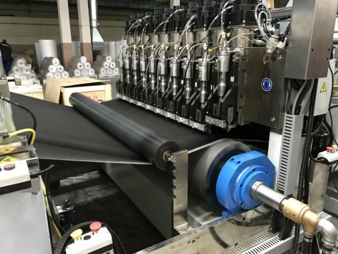
In the ultrasonic welding plant, two layers of nonwovens and one vaporpermeable film are merged with one another in a continuous lamination process to create roofing underlays. Vadzim Kavaliuk: “We have now been working with the system for more than two years and we are very happy with its performance and quality, as well as the consulting and service provided by Weber Ultrasonics.” © Weber Ultrasonics AG
High productivity, flexibility, process reliability, and energy efficiency
Just like filter materials used for mask making or in the dust filter sector, roofing underlays are typically produced from various layers of material that are bonded to one another to create a web-shaped product. This can be done using various processes. One of the largest European producers of nonwoven fabrics and their end products relies on ultrasonic welding with technology from Weber Ultrasonics.
Production of roofing underlays
Founded as a manufacturer of synthetic fibers back in 1964 in the then still Soviet Zavodskaya, OJSC Svetlogorkkhimvolokno is today one of the largest producers in this sector. Its production program encompasses a wide range of polyester textile yarns, carbon fibers, and heat-resistant polypropylene yarns. In addition to this, the Belarusian company produces various nonwovens from these synthetic fibers that can be adapted to meet the requirements of a wide range of applications thanks to their specific properties. Among others, these comprise products in the hygiene and medical engineering sectors, as well as the agriculture and construction industries. The latter includes roofing underlays, which a division of OJSC Svetlogorkkhimvolokno produces from two layers of nonwovens and a vapor-permeable film.
Lamination – a quality-critical step
The roofing underlays are produced to the specifications of the customers. They typically comprise one 20 micrometer thick, vapor-permeable film and two layers of nonwoven fabric, whose thickness varies. These three web materials are bonded to create a composite, which then passes through various quality checks, such as water column, abrasion resistance, and tear resistance testing.
For a long time, the quality-critical lamination step was performed exclusively using thermal processes, such as calendering and hot pressing.
The company also integrated ultrasonic welding as a laminating process for the first time in 2017 with a new production line for roofing underlays from the Taiwanese KNH Enterprise Co., Ltd. The ultrasonic components used for this were supplied by Weber Ultrasonics AG.
Vadzim Kavaliuk, Engineer for Investment Projects at OJSC Svetlogorkkhimvolokno:
“First of all, we did some testing with ultrasonic equipment from one Asian manufacturer and another European manufacturer. However, neither of these worked for our applications. Only the solution from Weber was able to meet our quality standards.”
Ultrasonic welding – more than an alternative
The high productivity, flexibility, and cost efficiency together provided the key impetus to go with the comparably young technology. Ultrasonic welding allows to laminate all of the company’s products with good results, regardless of the layer thickness.
The various layers of the roofing underlays are bonded to create a web for the continuous welding process. This web then runs into the gap on the structured roller at a defined angle. A converter converts the electrical signals generated by the ultrasonic generator into mechanical oscillations of the same frequency for the subsequent lamination process.
A booster and the actual welding tool, the sonotrode, are then used to apply these oscillations to the web that is to be bonded. The plastic molecules in the material are excited and melted by the frictional heat that occurs here.
The web is bonded under pressure to create a durable composite.
Thanks to its operating principle, ultrasonic welding eliminates the long heat-up times required for the rollers used in thermal and bonding processes. This not only saves energy, but also allows faster production.
In comparison with calendering, where radiant heat is applied over the entire surface, the web that is bonded with ultrasound is more flexible and softer, as well as free of deformations. In addition, there is no risk of overheating, which could otherwise lead to a fire. Since no adhesive is required, the rollers do not get soiled. Production interruptions for performing necessary cleaning work are therefore also a thing of the past.
Optimally matched ultrasonic technology and process design
The plant at OJSC Svetlogorkkhimvolokno for welding the 160 centimeter wide roofing underlays is designed for a throughput of 50 meters per minute. A total of ten ultrasonic systems were integrated to achieve this. The digital HS 4000 DIN rail generators employed each deliver 3.6 kW of power and, just like the converters, were designed specifically for continuous welding in non-stop operation.
To eliminate any risk of "streaks”, which not only represent a visual problem but generally also have a negative impact on quality, particular attention was given to the design of the welding tools. This design ensures that the unavoidable elongation of the sonotrodes due to thermal load is reliably compensated. At the same time, an overlap is achieved on the material in the welding process. This compensates for the gap which is required between the individual sonotrodes. The linear expansion encountered when feeding in the material, which causes the gap to change and thereby affects the welding result, represents a challenge with systems used for continuous ultrasonic welding. In this case, it was overcome by using a rigid and high-precision bearing mounting of the transducer. The solution, which has been proven in many applications, secures a constant gap and consistent force between the welding tool and the roller.
The angle and the tension with which the material web is fed into the plant has a decisive influence on the welding result.
Vadzim Kavaliuk:
“The design engineers from Weber Ultrasonics also used their many years of experience here. For example, they precisely stipulated the inlet and outlet angle for the various products, so that each product is wrapped optimally around the roller.”
Beside installation of a high-precision roller with a rod-shaped structure, whose bearing mountings were optimized, the tensions in the welding process were minimized using a nip roll. The fully automatic adjustment of the process parameters, such as the inlet gap as well as amplitude, contributes to the high ultrasonic welding quality of the various products. Product-specific programs are defined in the system control for this.
Doris Schulz